Подготовка поверхности
Оборудование для подготовки поверхности – основа качественного покрытия
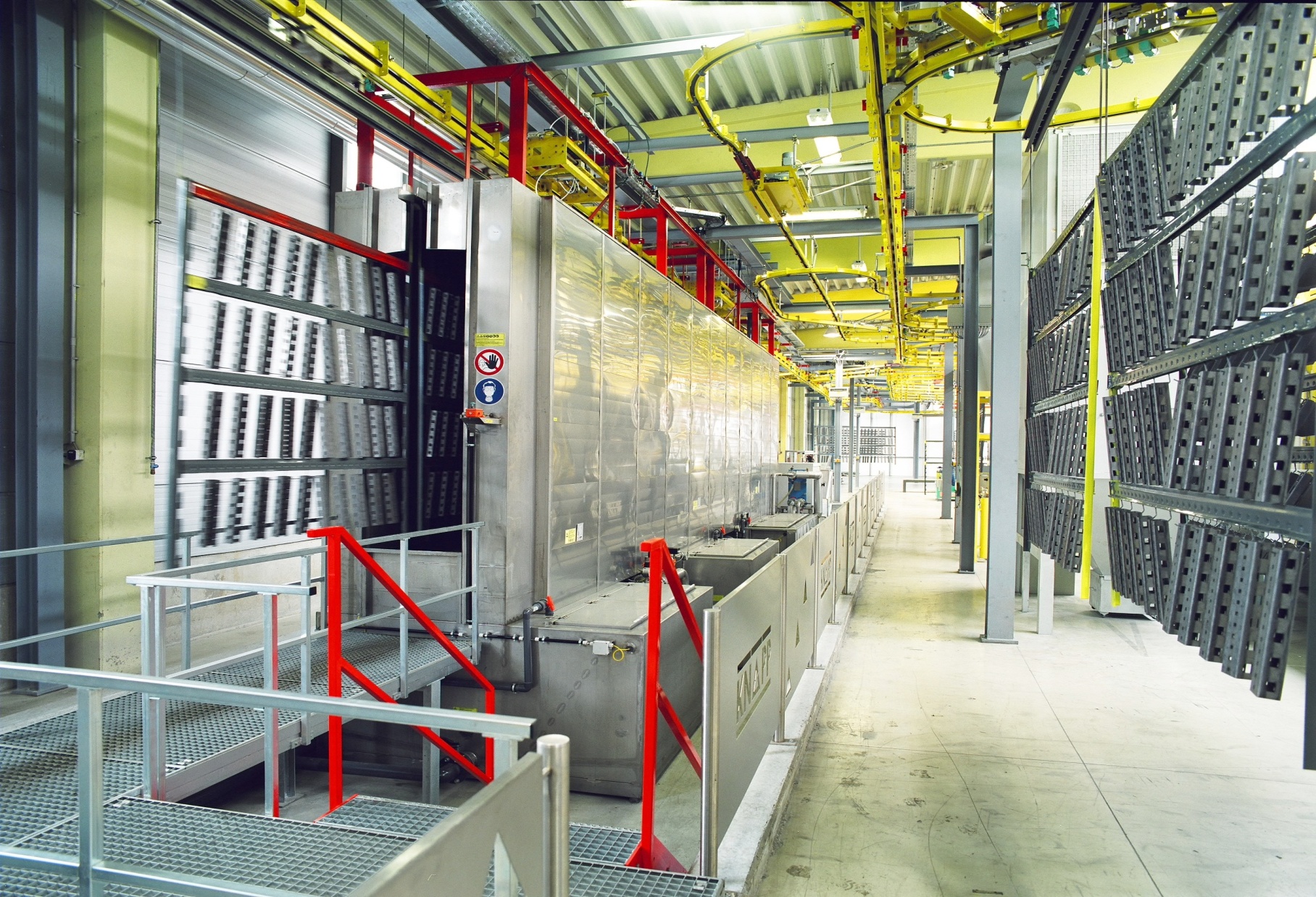
Основная задача оборудования подготовки поверхности удалить с поверхности окрашиваемого изделия различные загрязнения (масло, оксидные пленки, механические загрязнения), создать на поверхности дополнительный слой конверсионного покрытия, обеспечивающего дополнительную защиту от коррозии, высокую адгезию с покрытием.
Наши специалисты осуществят подбор, поставку и техническую поддержку оборудования для предварительной подготовки поверхности перед окраской. Проектирование и поставка оборудования для подготовки поверхности могут быть выполнены как в рамках поставки комплексной линии окраски, так и в форме отдельного компонента (включая транспортную систему, печь сушки деталей от влаги, шкаф управления).
Оборудование подготовки поверхности для окраски проектируется, исходя из:
- площади участка;
- габаритов окрашиваемых изделий;
- требований к покрытию;
- производственной программы;
- применяемых химических растворов (технология подготовки).
1. ХИМИЧЕСКАЯ ПОДГОТОВКА ПОВЕРХНОСТИ
Предназначена для полной очистки поверхности от жировых/масляных загрязнений, окислов, пыли методом обезжиривания или травления, создания дополнительных конверсионных защитных слоев.
Процессы химической подготовки:
- Обезжиривание (щелочное).
- Травление (кислотное).
- Железное фосфатирование. Создает конверсионный слой улучшающий адгезию, замедляет распространение коррозии.
- Цинковое фосфатирование. Создает конверсионный слой улучшающий адгезию, блокирует распространение коррозии на протяжении длительного времени.
- Хроматирование (для алюминия и его сплавов). Создает поверхностный слой, блокирующий возникновение оксидной пленки на поверхности детали.
- Пассивация. Создает тонкую фазовую плёнку, обеспечивающую высокую коррозионную стойкость и лучшую адгезию. Современные технологии предусматривают использование безхроматных химикатов для пассивации.
- Другие.
Технологический процесс, количество стадий подготовки определяются в зависимости от требований, предъявляемых к покрытию, материала изделия, сферы его применения, применяемых химических растворов.
Пример расчета оборудования подготовки поверхности для изделий из стали
Внутри помещения | Желаемый срок службы покрытия | |||
<= 2 лет | 2...5 лет | 3-6 лет | 5-8 лет | |
Эпоксидные порошковые краски | Ручная очистка или обезжиривание /железное фосфатирование + промывка | Обезжиривание /железное фосфатирование + промывка 1/2 + финальная промывка дем.водой <=200µS/cm | Обезжиривание /железное фосфатирование + промывка 1/2 + финальная промывка дем.водой <=20µS/cm | |
Полиэфирные порошковые краски | Ручная очистка или обезжиривание/железное фосфатирование + промывка | Обезжиривание /железное фосфатирование + промывка 1/2 | Обезжиривание /железное фосфатирование + промывка 1/2 + финальная промывка дем.водой <=200µS/cm | Обезжиривание /железное фосфатирование + промывка 1/2 + финальная промывка дем.водой <=20µS/cm |
Вне помещения | Желаемый срок службы покрытия | |||
<= 2 лет | 2...5 лет | 3-6 лет | 5-8 лет | |
Эпоксидные порошковые краски | Обезжиривание /железное фосфатирование + промывка 1/2 + финальная промывка дем.водой <=200µS/cm | Обезжиривание /железное фосфатирование + промывка 1/2 + финальная промывка дем.водой <=20µS/cm | Обезжиривание /железное фосфатирование + промывка 1/2 + пассивация промывка +финальная промывка дем.водой <=10µS/cm | |
Полиэфирные порошковые краски | Обезжиривание /железное фосфатирование + промывка 1/2 + финальная промывка дем.водой <=200µS/cm | Обезжиривание /железное фосфатирование + промывка 1/2 + финальная промывка дем.водой <=20µS/cm | Обезжиривание /железное фосфатирование + промывка 1/2 + пассивация промывка +финальная промывка дем.водой <=10µS/cm | Обезжиривание + промывка 1 + Активация + цинковая фосфатирование +промывка 1/2 + финальная промывка дем.водой <=10µS/cm |
Для подготовки поверхностей изделий из алюминия и его сплавов используют так же более сложный процесс подготовки поверхности с использованием травления, безхромной пассиваций или хроматирования
Цинк и его сплавы при необходимости покрываются хроматом цинка или фосфатом цинка.
Детали из магния обрабатываются с помощью хроматирования.
ТЕХНОЛОГИЯ ХИМИЧЕСКОЙ ПОДГОТОВКИ ПОВЕРХНОСТИ
НАГРЕВ ХИМИЧЕСКИХ РАСТВОРОВ
Для различных технологических процессов химической подготовки поверхности используются химические растворы, которые имеют различную рабочую температуру.
Традиционные процессы обезжиривания/железного фосфатирования используют, как правило, химический раствор с рабочей температурой 50-60°С. Использование химических растворов нового поколения требует гораздо меньшей рабочей температуры растворов.
Для нагрева в зависимости от пожеланий заказчика может использоваться природный или сжиженный газ, дизельное топливо, электричество или комбинированные решения (газ/дизельное топливо).
Способ нагрева может быть различным:
- через встроенные в ванны теплообменники;
- через выносные (внешние) пластинчатые теплообменники;
- термоэлектрические нагреватели.
Как правило, встроенные теплообменники нагревают химрастворы посредством встроенных ТЭН или горелок. При использовании внешнего пластинчатого теплообменника требуется подача горячей воды с температурой 70-90°С от внешнего источника, например, от бойлера.
2. МЕХАНИЧЕСКАЯ ПОДГОТОВКА ПОВЕРХНОСТИ
Используется для удаления механических загрязнений, в том числе следов сварки, окалины, следов коррозии. В основном механическую подготовку применяют для крупногабаритных изделий или деталей, для которых применение химических растворов неэффективно или недопустимо. В качестве оборудования механической обработки поверхности используются дробеметы (дробеструи) и/или оборудование для обработки сухим льдом.
ЭНЕРГОСБЕРЕЖЕНИЕ
Все технологические аспекты, которые активно влияют на снижение энергозатрат, учтены в нашем оборудовании.
- Температура при обработке поверхности должна быть как можно ниже.
- Зоны увеличенной длины обработки химраствором позволяют снизить температуру в ваннах.
- Зоны стекания увеличенной длины.
- Термоизоляция туннелей и ванн.
- Применение форсунок, не образующих тумана (малый уровень тонкого распыла) – меньше образование капель, меньшая активность поверхности. Из горячей зоны выходит меньше пара. Выше кинетическое воздействие на поверхность детали – выше КПД. Это означает, что при той же самой энергии столкновения струи жидкости с деталью потребуется более низкой давление. На практике, вместо насоса на 20 кВт с давлением 2,2 бар можно использовать насос мощностью 15 кВт. Экономия энергии до 35%.
- Применение шаровых форсунок с оптимальными углами распыления и низким давлением во избежание туманообразования.
- Применение многократной каскадной схемы использования воды.
- Применение внешних теплообменников для нагрева ванн. Больше термический КПД по сравнению с встроенными теплообменниками. Ниже эксплуатационные расходы.